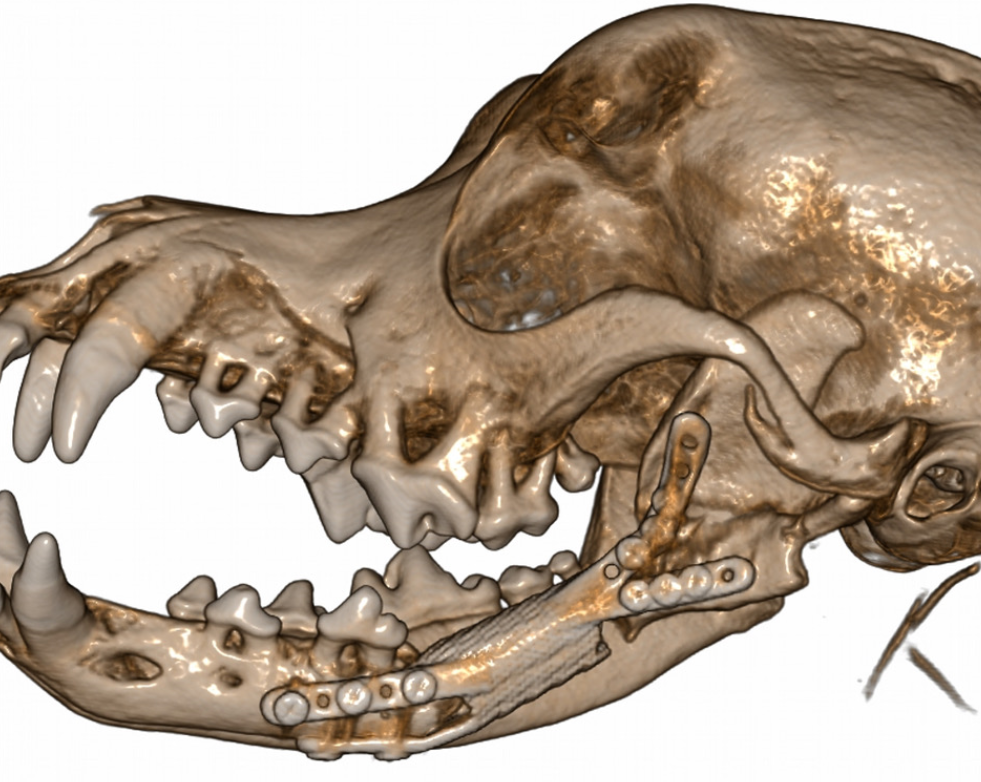
Spersonalizowane implanty weterynaryjne są coraz częściej stosowane w leczeniu wad spowodowanych urazami lub resekcją kości. Ze względu na fakt, że pacjenci w zależności od rasy mają inną budowę anatomiczną, trudno jest zaprojektować implanty, które będą pasować do wszystkich przypadków klinicznych. Indywidualne projektowanie zapewnia stworzenie implantu, który jest dopasowany do anatomicznego kształtu kości danego pacjenta. Najbardziej atrakcyjną metodą wytwarzania złożonych implantów na podstawie danych z tomografii komputerowej są techniki wytwarzania addytywnego (AM), takie jak Fused Deposition Modeling (FDM) i Selective Laser Melting (SLM). W zależności od zamierzonego zastosowania można wytwarzać tymi metodami zarówno implanty polimerowe jak i metalowe.
Stworzono model implantu, który był idealnie dopasowany do anatomicznego kształtu w obszarze brakującej kości.
Mocowanie implantu do kości żuchwy, zostało zapewnione przez płytki mocujące dostosowane do kształtu kości pacjenta. Płytki stanowiły integralną część implantu i były wytwarzane w tym samym procesie (rys. 1).
Rys. 1. Model spersonalizowanego implantu żuchwy przed i po zaprojektowaniu płyt mocujących
Objętość implantu charakteryzowała się strukturą o otwartej porowatości, aby zmniejszyć masę i umożliwić wrastanie kości wewnątrz implantu. Ponadto, struktura ta umożliwia dostosowanie modułu Younga implantu do modułu kości. Zbliżone wartości modułów Younga implantu i kości, pozwalają uniknąć efektu ekranowania naprężeń, który prowadzi do naturalnej demineralizacji kości w otoczeniu implantu (rys. 2).
Rys. 2. Perforowana struktura implantu o otwartej porowatości
Zaprojektowane struktury zostały wyprodukowane z czystego proszku tytanowego przy wykorzystaniu techniki selektywnego topienia laserowego (SLM) (rys. 3).
Rys. 3. Schemat wytworzenia spersonalizowanego implantu
Podczas procesu SLM materiał w postaci cienkiej warstwy proszku jest rozprowadzany na platformie roboczej, a następnie topiony za pomocą lasera na podstawie danych CAM (Computer Aided Manufacturing), czyli danych CAD (Computer Aided Design), wzbogaconych o strategie pracy lasera. Po stopieniu pierwszej warstwy proszku stół roboczy jest obniżany o określoną wysokość, która jest równa grubości warstwy modelu CAD, zwykle kilkudziesięciu mikrometrów.
Rys. 4. Gotowy implant przed sterylizacją
Implant został wyprodukowany przy użyciu parametrów produkcyjnych, które zapewniają wysoką dokładność produkcji skorelowaną z modelem CAD (Rys. 5.).
Rys. 5. Zdjęcie RTG okolic żuchwy po wykonaniu wszczepienia
Operacja chirurgiczna została przeprowadzona przez lekarza weterynarii, który umieścił implant w brakującym fragmencie żuchwy. Implant z płytkami mocującymi był idealnie dopasowany do kości. Nie odnotowano powikłań pooperacyjnych. Po rekonwalescencji pacjenta wykonano tomografię komputerową (Rys. 6.). Okazało się, że implant był dobrze dopasowany do żuchwy, właściwie umocowany i nie przemieszczał się w żadnym kierunku.
Ponadto zaobserwowano, że po operacji pacjent był w stanie spożywać pokarm, a więc została przywrócona pełna sprawność żuchwy.
Rys. 6. Model 3d wykonany na podstawie tomografii komputerowej po rekonwalescencji
Spersonalizowane implanty weterynaryjne przeznaczone dla konkretnego pacjenta można z powodzeniem wytwarzać technikami druku 3D z materiałów biokompatybilnych. Odpowiednie parametry produkcyjne zapewniają odpowiednią dokładność wytwarzanego elementu skorelowanego z modelem CAD. Drukowane biokompatybilne implanty tytanowe 3D są akceptowane przez organizm pacjenta i nie powodują żadnych powikłań pooperacyjnych.
Źródła: https://www.facebook.com/KlinikaArka/
Stworzono model implantu, który był idealnie dopasowany do anatomicznego kształtu w obszarze brakującej kości.
Mocowanie implantu do kości żuchwy, zostało zapewnione przez płytki mocujące dostosowane do kształtu kości pacjenta. Płytki stanowiły integralną część implantu i były wytwarzane w tym samym procesie (rys. 1).
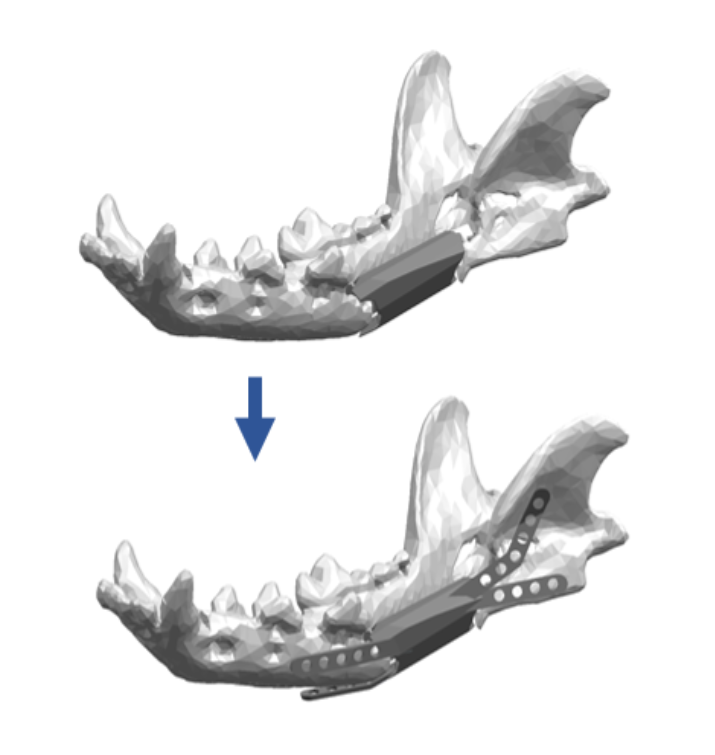
Objętość implantu charakteryzowała się strukturą o otwartej porowatości, aby zmniejszyć masę i umożliwić wrastanie kości wewnątrz implantu. Ponadto, struktura ta umożliwia dostosowanie modułu Younga implantu do modułu kości. Zbliżone wartości modułów Younga implantu i kości, pozwalają uniknąć efektu ekranowania naprężeń, który prowadzi do naturalnej demineralizacji kości w otoczeniu implantu (rys. 2).
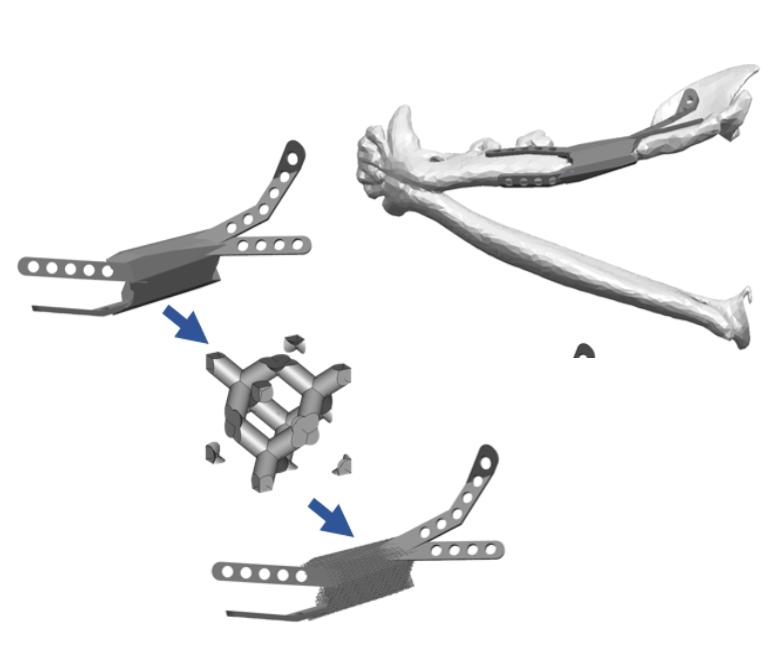
Zaprojektowane struktury zostały wyprodukowane z czystego proszku tytanowego przy wykorzystaniu techniki selektywnego topienia laserowego (SLM) (rys. 3).
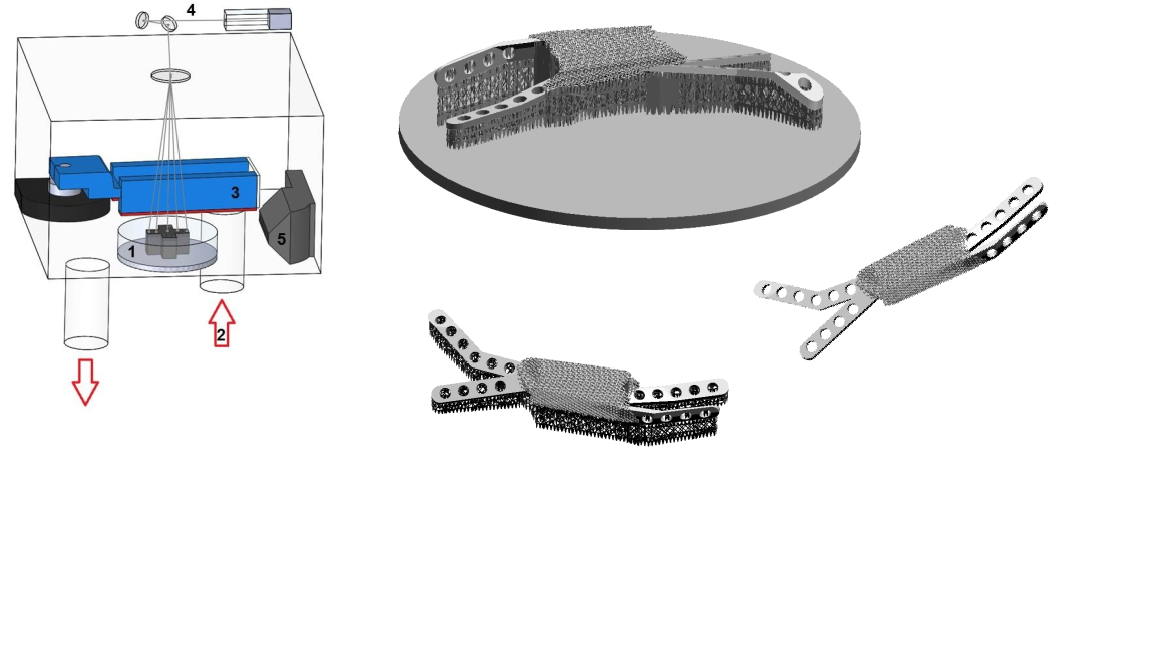
Podczas procesu SLM materiał w postaci cienkiej warstwy proszku jest rozprowadzany na platformie roboczej, a następnie topiony za pomocą lasera na podstawie danych CAM (Computer Aided Manufacturing), czyli danych CAD (Computer Aided Design), wzbogaconych o strategie pracy lasera. Po stopieniu pierwszej warstwy proszku stół roboczy jest obniżany o określoną wysokość, która jest równa grubości warstwy modelu CAD, zwykle kilkudziesięciu mikrometrów.
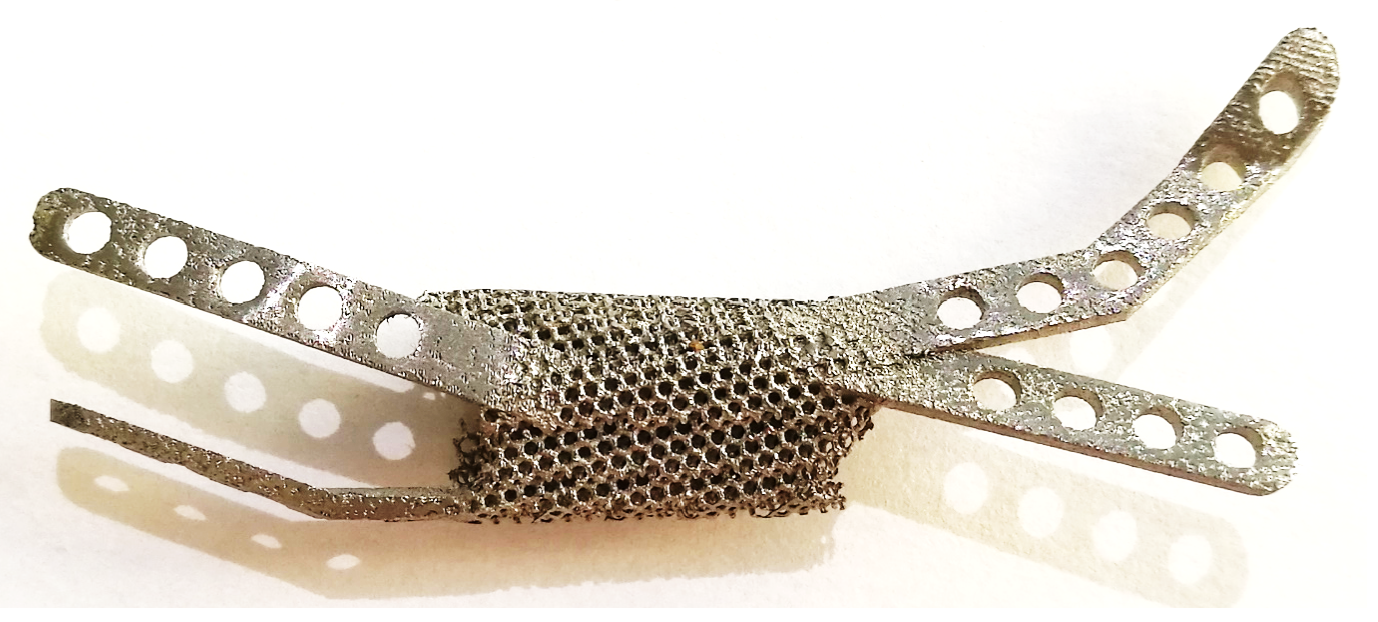
Implant został wyprodukowany przy użyciu parametrów produkcyjnych, które zapewniają wysoką dokładność produkcji skorelowaną z modelem CAD (Rys. 5.).
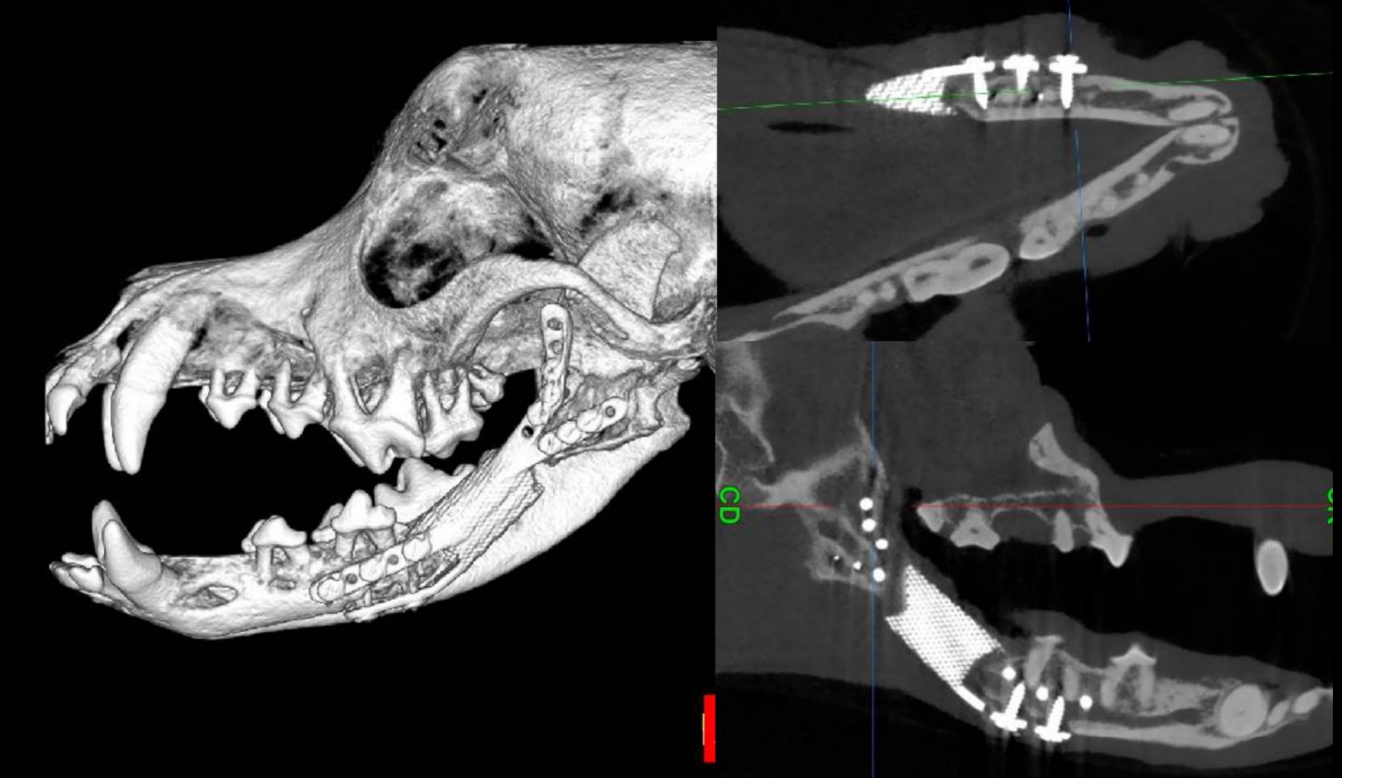
Operacja chirurgiczna została przeprowadzona przez lekarza weterynarii, który umieścił implant w brakującym fragmencie żuchwy. Implant z płytkami mocującymi był idealnie dopasowany do kości. Nie odnotowano powikłań pooperacyjnych. Po rekonwalescencji pacjenta wykonano tomografię komputerową (Rys. 6.). Okazało się, że implant był dobrze dopasowany do żuchwy, właściwie umocowany i nie przemieszczał się w żadnym kierunku.
Ponadto zaobserwowano, że po operacji pacjent był w stanie spożywać pokarm, a więc została przywrócona pełna sprawność żuchwy.
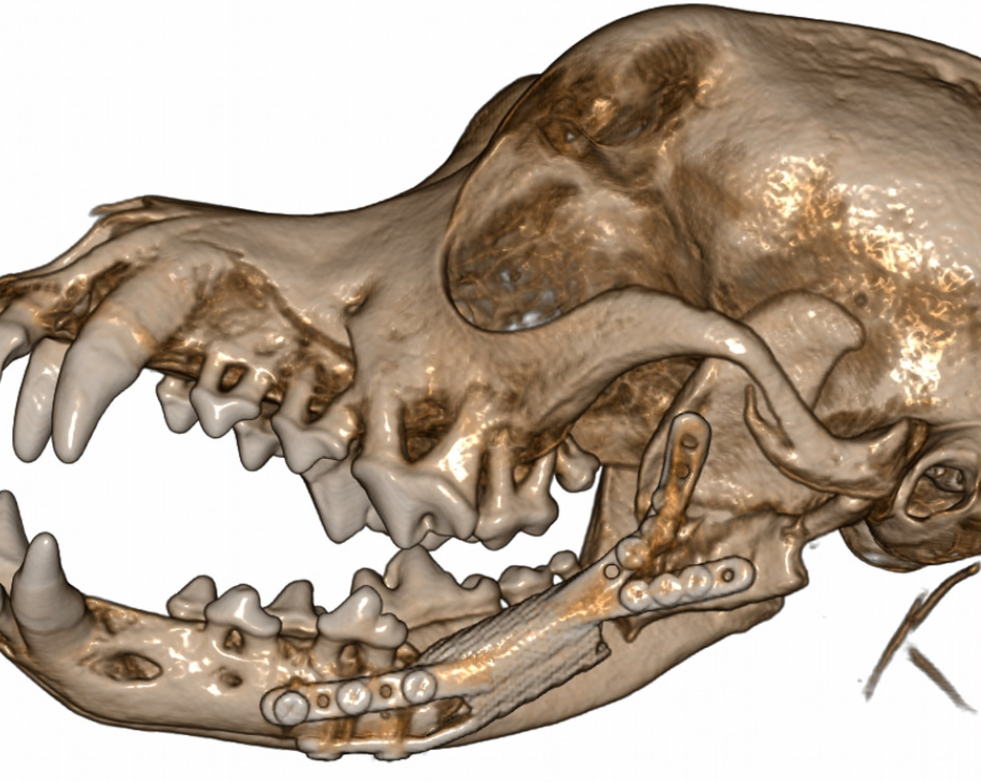
Spersonalizowane implanty weterynaryjne przeznaczone dla konkretnego pacjenta można z powodzeniem wytwarzać technikami druku 3D z materiałów biokompatybilnych. Odpowiednie parametry produkcyjne zapewniają odpowiednią dokładność wytwarzanego elementu skorelowanego z modelem CAD. Drukowane biokompatybilne implanty tytanowe 3D są akceptowane przez organizm pacjenta i nie powodują żadnych powikłań pooperacyjnych.
Źródła: https://www.facebook.com/KlinikaArka/